Yes, But Here’s Why It May Not Be a Good Idea…
If you own a commercial property and are considering installing TPO (Thermoplastic Olefin) over your metal roof, you might want to think twice. While it is technically possible to lay TPO over a metal roof, there are several significant drawbacks that could cost you in the long run, especially if you plan on keeping your property for more than 10 years. In fact, opting for an alternative option may be the better solution, and here’s why.
1. The Hidden Moisture Problem: Microclimates and Rust
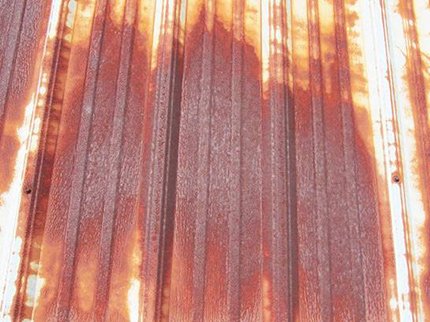
When TPO is installed over metal roofs, insulation is often placed between the metal ribs to create a flat surface. What many don’t realize is that this setup creates a microclimate between the metal and the TPO membrane. Over time, this leads to moisture buildup, which can go unnoticed for years.
The worst part? The trapped moisture can cause rust to form under the TPO membrane. This rust can eat away at the metal panels, and by the time you discover the issue, you could be looking at severe damage to your roof—and even structural damage to your building. Addressing these problems later can be a nightmare, requiring extensive repairs that are much more expensive than preventive solutions like fluid-applied coatings.
2. TPO Roofs Still Have Seams, and Seams Fail
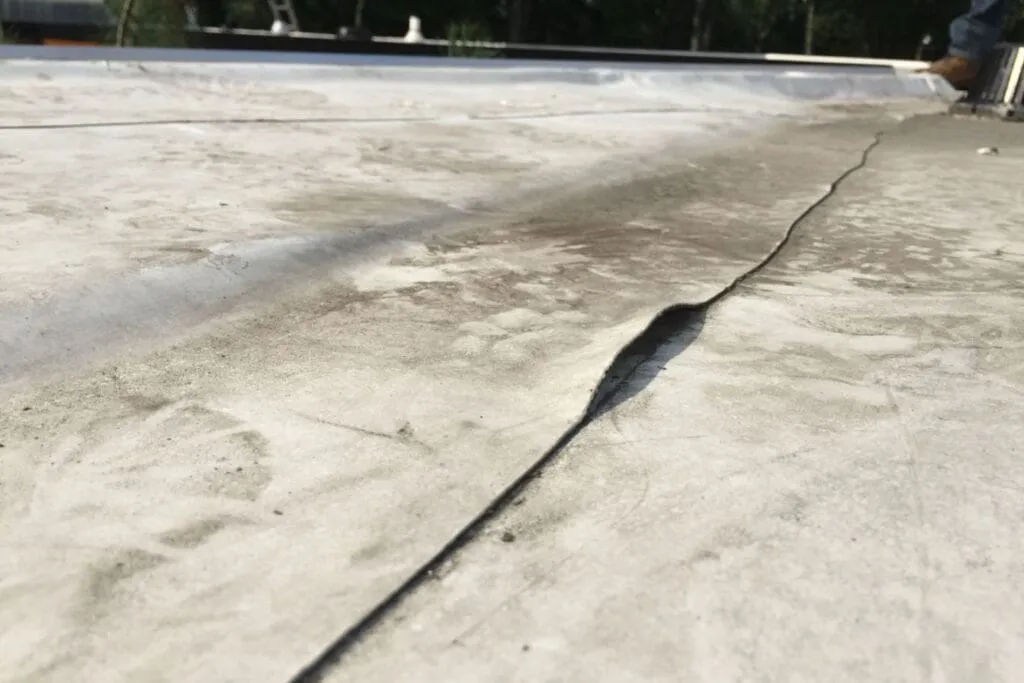
One of the biggest selling points of TPO roofing is its waterproof membrane. However, TPO roofs are not seamless, and every seam is a potential point of failure. As the roof ages, the seams can separate, crack, or weaken, leading to leaks. Over time, these leaks can cause damage to the roof and the underlying structure, resulting in expensive repairs and water damage to the building’s interior.
3. Lamination Problems: Cracking and Shrinkage
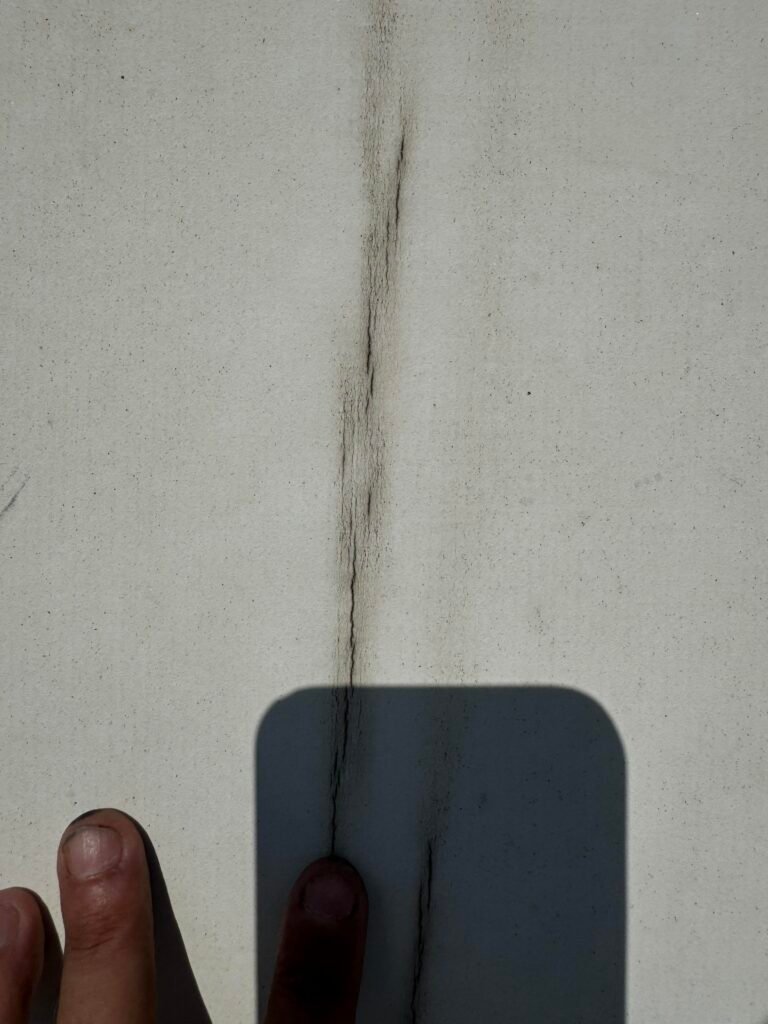
TPO membranes are laminated, meaning they have a layered structure. The top layer is particularly vulnerable to wear and tear. As the roof ages, the lamination can begin to crack or shrink, creating weak points that expose your roof to the elements. Shrinkage around edges or details like vents and skylights is especially problematic and can lead to water infiltration.
4. High Temperatures Can Make TPO Brittle
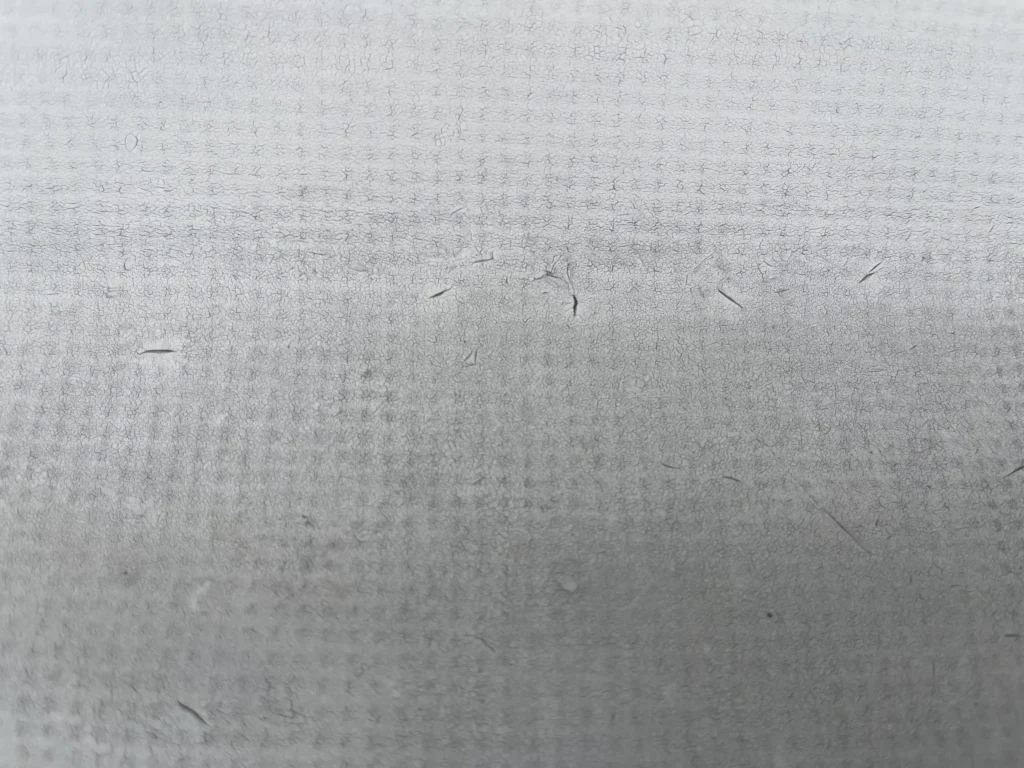
In regions with high temperatures, TPO roofing is known to shrink and become brittle. This causes even more stress on the seams and weak points, accelerating the aging process and the need for repairs. If your property is in an area that experiences extreme heat, this is definitely something to keep in mind.
5. Limited Lifespan: 15-20 Years
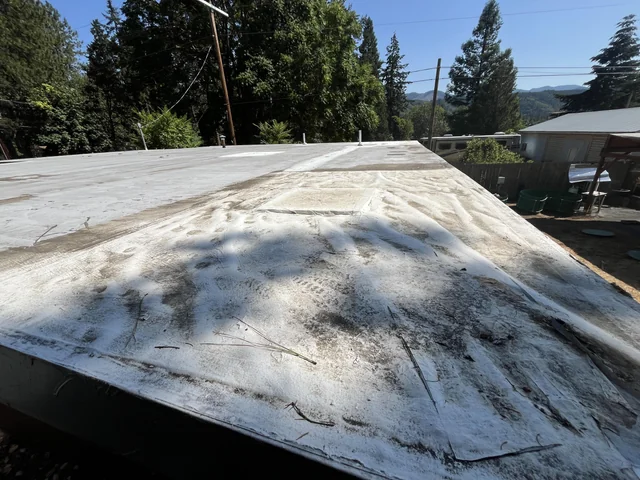
While TPO roofs are marketed as durable, their lifespan typically ranges between 15 and 20 years, depending on the climate and maintenance. If you’re planning on keeping your property long-term, this means you’ll likely face another roofing project sooner than you’d expect. Plus, as the roof ages, it will require more frequent repairs to address issues like punctures, leaks, and shrinkage.
6. Prone to Punctures
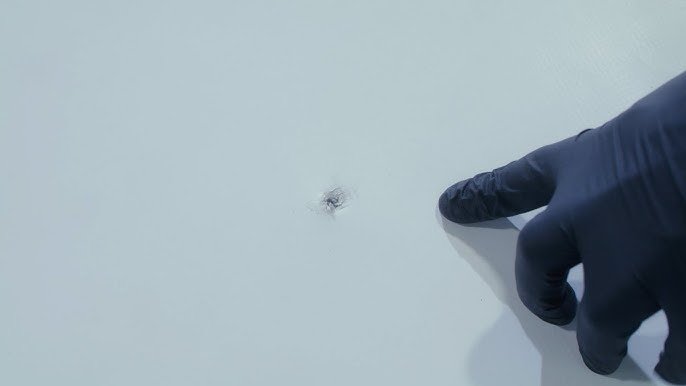
Unlike fluid-applied coatings, which offer a monolithic, seamless membrane, TPO is more susceptible to punctures. Whether it’s heavy foot traffic, dropped tools, or falling debris like tree limbs, TPO’s single-ply membrane can be damaged relatively easily, leading to costly repairs or even a full replacement.
7. Fire Risk
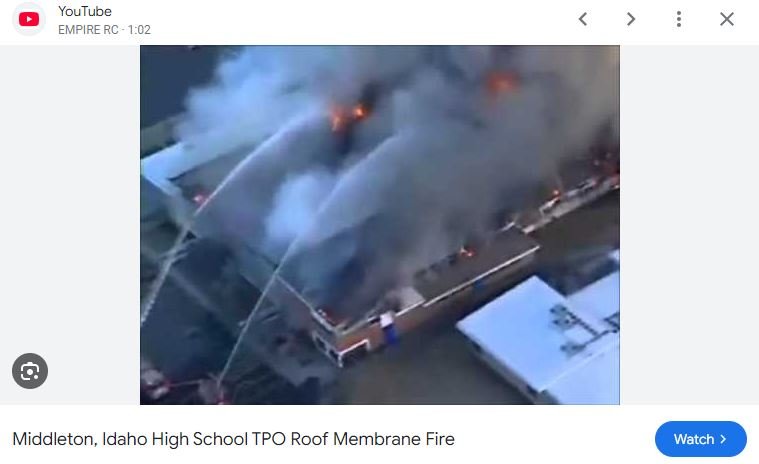
Although TPO membranes do have some fire-resistant properties, they can still be susceptible to ignition if they are not treated with fire-retardant additives. In the event of a nearby fire, flying embers could land on the roof and cause significant damage. This is another risk that property owners should not overlook when considering roofing options.
So, What’s the Better Option? Fluid-Applied Roof Coating
At Bold Commercial Roofing, we believe in providing long-term, cost-effective solutions for our clients. Instead of taking on the risks that come with laying TPO over metal roofs, we recommend a fluid-applied roof coating.
Here’s why:
-
- Seamless Application: Fluid-applied coatings create a completely seamless, watertight membrane that eliminates the risks of seam failure.
-
- Rust Prevention: By sealing the roof in a protective, durable coating, you eliminate the risk of rust forming from trapped moisture.
-
- Longer Lifespan: Our fluid-applied coatings are designed to last decades with minimal maintenance.
-
- Energy Efficiency: Many fluid-applied coatings have high reflectivity, which helps reduce energy costs by reflecting sunlight away from your building.
-
- Cost-Effective: Over time, fluid-applied coatings are far more cost-effective compared to replacing TPO or dealing with hidden damage from moisture and rust. Generally speaking, fluid applied roof coatings are around 50% or less than the cost of replacement.
-
- Fully Tax Deductible: 100% of the cost of the roof restoration is eligible for tax credit, spend 100k on your roof, knock off 100k of earned income on your taxes year 1! *Not a financial advisor, contact your CPA for confirmation.
-
- Save on A/C Bills: Most clients state that they are enjoying around a 30% reduction in their air conditioning bill during the hot months.
Don’t wait until it’s too late. If you’re considering upgrading your commercial roof, contact Bold Commercial Roofing today for a free consultation. We’ll help you choose the best solution for your property, ensuring you avoid unnecessary costs and headaches down the road.
Contact Us
Phone: 417-222-7535
Email: info@boldcommercialroofing.com
Website: www.boldcommercialroofing.com
Let’s protect your property with a solution built to last!